Chem-Pruf fiberglass door systems are manufactured completely by hand utilizing only the highest quality raw materials. Not only is this unrivaled method of manufacture far superior, it allows the flexibility to customize the door systems to meet unique requirements.
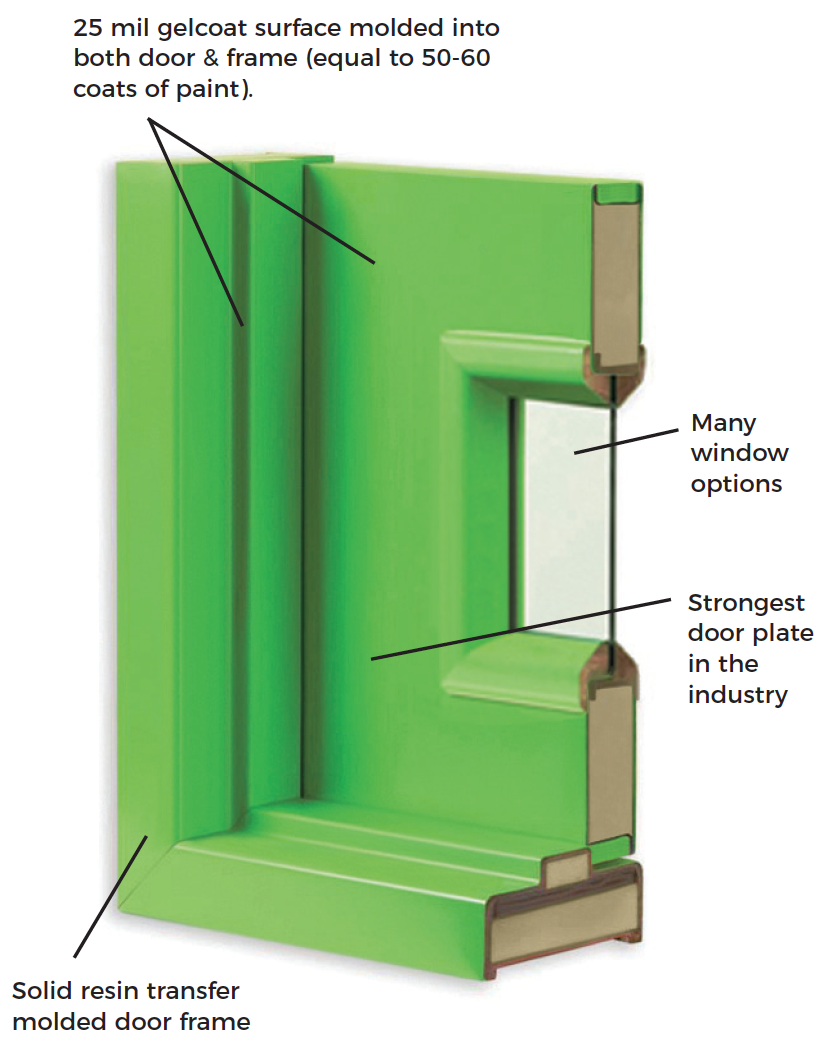
Gelcoat
Gelcoat (pigmented fiberglass resin) serves as the color and finish of the product and most importantly provides an impenetrable barrier against corrosive chemical and environmental attack. The application of the color is the first step of our manufacturing process. 25 mil gelcoat is integrally molded in every Chem-Pruf door. No other manufacturer has the experience that Chem-Pruf does when it comes to manufacturing all fiberglass door systems. Plus, Chem-Pruf, when requested, can provide a fiberglass gelcoat for FDA/USDA applications, High UV resistance and High Gloss properties.
Plates
Chem-Pruf door plates are by far the strongest in the industry, measuring 0.125 inches thick and weighing 1.0 Ib/ft². Once the gelcoat has been applied, these plates are hand laid and integrally molded in one continuous piece using high quality resins tailored to the specific environment and approximately 5 ounces of glass per square foot. For maximum corrosion resistance, Chem-Pruf maintains a glass content between 25% and 35% yielding a glass-to-resin ratio of about 1:3. Not only are these plates impervious to corrosive attack, they provide outstanding protection against impact caused by high wind debris. Just the plate alone was tested; it met and surpassed the large missile impact requirements of the Florida Building Code TAS 201-94 and ASTM E 1886/1996 Level D.
Stiles and Rail
The stile and rail is commonly referred to as the collar of the door. The way Chem-Pruf designed and manufactures the stile and rail in one continuous piece (no miter corners) is what creates the seamless edge of the door and a solid structure to bond the plates. This one continuous piece design was so unique and ingenious that it was issued the first patent ever issued by the U.S. Patent Office for an atmospheric resistant door.
Cores
The interior cavity of the fiberglass door is completely filled with a corrosion-resistant material. The type of core that is used, such as Polypropylene Honeycomb (PPC), Polyisocyanurate Foam, or Mineral, is determined either by application or specification. Alternate core material designs that accommodate sound ratings or blast ratings are all available at your request.
Bonding
Chem-Pruf has developed a proprietary bonding resin system to fuse the plates to the collar and core, creating one homogeneous, engineered structure that ensures the strongest interface possible. In this manner, there will be no separation or delamination of a Chem-Pruf fiberglass door – GUARANTEED